
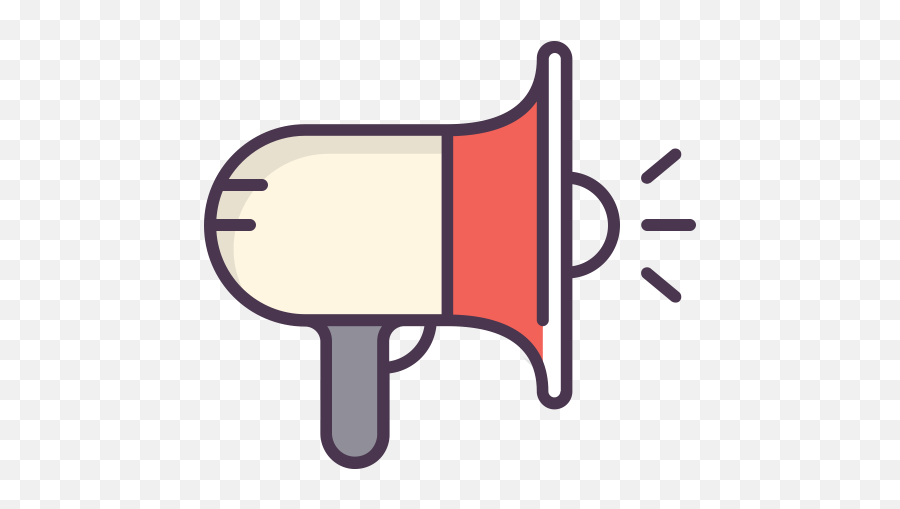
Requirements governing respirator selection, use, maintenance and inspection across Canada.
You must take measures to prevent workers from breathing in harmful mists, vapours, fumes, gases, dusts and other airborne contaminants. The best way to accomplish that objective is at the source by keeping contaminants out of the air in the first place, such as via elimination of hazardous products or mechanical ventilation. Regrettably, such solutions may not be reasonably practicable. In that situation, respiratory protection equipment becomes the critical line of defence. As safety coordinator, you must ensure that selection, use and maintenance of respiratory protective equipment meet the OHS requirements of your jurisdiction. Here’s a summary of the laws you need to be aware of to meet that challenge regardless of where in Canada you operate.
Abbreviations: In this summary:
- IDLH means an atmosphere that is immediately dangerous to life or health
- CSA Z94.4 means CSA Group Standard Z94.4, Selection, Use, and Care of Respirators;
- CSA Z180.1 means CSA Group Standard Z180.1, Compressed Breathing Air and Systems;
- CSA Z1610 means CSA Group Standard Z1610, Protection of First Responders from Chemical, Biological, Radiological, and Nuclear (CBRN) Events
- NFPA 1971 means NFPA 1971, Standard for Protective Ensemble for Fire Fighting
- NFPA 1981 means NFPA 1981, Standard on Open-Circuit Self-Contained Breathing Apparatus for Fire Fighters
- NFPA 1982 means NFPA 1982, Standard on Personal Alert Safety Systems (PASS) for Fire Fighters
Respiratory Protective Equipment
FEDERAL
Code of Practice/Program: Not specifically required
Equipment: 1. If there’s a risk of injury or disease due to exposure to an airborne hazardous substance, other than a chemical, biological, radiological or nuclear (CBRN) agent, or an oxygen-deficient atmosphere in a workplace, employer must provide every person granted access to the workplace respiratory protection equipment that provides adequate protection from hazard and doesn’t in itself create a hazard that: (a) Is listed in the US NIOSH Certified Equipment List; (b) CSA Z94.4; and (c) Protects the respiratory tract against the hazardous substance or oxygen deficiency, as the case may be [COHS Regs, Sec. 12.13(1)]; 2. If there’s a risk of injury or disease from exposure to CBRN agents, employer must provide every person granted access to workplace respiratory protection equipment for protection against those CBRN agents that: (a) In the case of a first responder, meets CSA Z1610; and (b) In any other case: (i) is listed in the NIOSH Certified Equipment List, and meets the requirements of CSA Z94.4, or (ii) meets the requirements of CSA Z1610 [COHS Regs, Sec. 12.13(3)] 3. Air Supplying Respirator systems and breathing air must meet CSA Z180.1 [COHS Regs, Sec. 12.13(2)]
Use and Maintenance: All respiratory protective equipment provided by an employer must be: (a) Used, stored and maintained in accordance with CSA Z94.4; (b) Inspected and, if necessary, tested by a qualified person in accordance with the manufacturer’s instructions to ensure it’s in good operating condition; (c) Safely and properly fitted to each user by a qualified person in accordance with the manufacturer’s instructions; and (d) Maintained in a clean and sanitary condition by a qualified person in accordance with the manufacturer’s instructions [COHS Regs, Sec. 12.05]
Training: Employer must ensure that: (a) Every person who uses protection equipment gets instruction by a qualified person in use of that equipment; (b) In addition to such instruction, if the user is an employee he/she must also get instruction and training by a qualified person in the operation and maintenance of the equipment and training by a qualified person in its use; and (c) Such instruction and training is summarized in writing and that a copy of the summary is readily available for consultation by every person granted access to the workplace [COHS Regs, Sec. 12.2]
Records: (a) Employer must keep a record of all protective equipment it provides (other than disposable equipment) that contains: (i) a description of the equipment and the date the employer acquired it, (ii) the date and result of each inspection and test of the equipment, (iii) the date and nature of any maintenance work performed on the equipment since the employer acquired it, and (iv) the name of the person who performed the inspection, test or maintenance; and (b) Record must be kept at the workplace where the equipment is located for 2 years beginning on the day on which the equipment is permanently removed from service (unless another section of the regulations require a longer retention period) [COHS Regs, Sec. 12.21]
ALBERTA
Code of Practice/Program: (a) If respiratory protective equipment is used at work site, employer must prepare a code of practice governing the selection, maintenance and use of respiratory protective equipment; (b) If a health care worker is exposed to airborne biohazardous material, code of practice must include training on at least an annual basis [OHS Code, Sec. 245]
Equipment: (a) General: Employer must ensure that required respiratory protective equipment is approved by NIOSH or another organization approved by a Director of Occupational Hygiene [OHS Code, Sec. 246]; (b) Breathing Air: Employer must ensure that the quality of air used in a self-contained breathing apparatus or air line respirator: (i) meets the requirements of Table 1 of CSA Z180.1-00 (R2005), and (b) doesn’t contain a substance in a concentration above 10% of its occupational exposure limit [OHS Code, Sec. 249]; (c) IDLH: Employer must ensure worker wears self-contained breathing apparatus or an air line respirator that (i) is of a type that will maintain positive pressure in the face piece, (ii) has a capacity of at least 30 minutes unless the employer’s hazard assessment indicates the need for a greater capacity, (iii) provides full face protection in situations where contaminants may irritate or damage the eyes, (iv) in the case of an air line respirator, is fitted with an auxiliary supply of respirable air of sufficient quantity to enable the worker to escape from the area in an emergency, and (v) in the case of a self-contained breathing apparatus, has an alarm warning of low pressure [OHS Code, Sec. 251]; (d) Non-IDLH: Employer must ensure that a worker wears self-contained breathing apparatus or an air line respirator having a capacity of at least 30 minutes if: (i) the employer determines that conditions at the work site aren’t or can’t become IDLH but either: (x) the oxygen content of the atmosphere is or may be less than 19.5% by volume, or (y) the concentration of airborne contaminants exceeds or may exceed that specified by the manufacturer for air purifying respiratory equipment, and (ii) the complete equipment required for IDLH isn’t provided [OHS Code, Sec. 252]; (e) Air purifying equipment: Employer may allow workers to wear air purifying respiratory protective equipment if: (i) the oxygen content of the air is, and will remain, 19.5% or greater by volume, (ii) the air purifying equipment used is designed to protect against the specific airborne contaminant(s) present, and (iii) the concentration of airborne contaminants doesn’t exceed the maximum concentration specified by the manufacturer for the specific type of air purifying equipment, taking into consideration the duration of its use [OHS Code, Sec. 253]; (f) Emergency escape equipment: If normal operating conditions don’t require wearing of respiratory protective equipment but emergency conditions may occur requiring a worker to escape from the work area, the employer may allow the escaping worker to wear: (i) a mouth bit and nose-clamp respirator if (x) the respirator is designed to protect the worker from the specific airborne contaminants present, and (y) the oxygen content of the atmosphere during the escape is 19.5 percent or greater by volume, or (ii) alternative respiratory protective equipment that can be proven to give the worker the same or greater protection [OHS Code, Sec. 254]; (g) Abrasive blasting: Employer must ensure that worker performing abrasive blasting wears a hood specifically designed for abrasive blasting, supplied with air at a positive pressure of no more than 140 kilopascals [OHS Code, Sec. 255]
Use and Maintenance: Employer must ensure that respiratory protective equipment is: (a) Used, stored and maintained in accordance with CSA Z94.4; (b) Stored in a readily accessible location in a manner that prevents contamination; (c) Maintained in a clean and sanitary condition; (d) Inspected before and after each use to ensure it’s in satisfactory working condition; and (e) Serviced and used in accordance with the manufacturer’s specifications [OHS Code, Sec. 248]
Fit Testing: Employer must ensure that: (a) Respiratory protective equipment that depends on an effective facial seal is correctly fit tested and tested in accordance with CSA Z94.4-02; and (b) Workers required to wear respiratory protective equipment that depends on an effective facial seal are clean shaven where the face piece of the equipment seals to the skin of the face [OHS Code, Sec. 250]
Training: Worker must be trained in the correct use, care, limitations and assigned maintenance of the personal protective equipment [OHS Code, Sec. 228(1)]
Records: Not specified
BRITISH COLUMBIA
Code of Practice/Program: (a) If PPE is required to protect against chemical exposure or oxygen deficient atmosphere, employer must implement an effective protective equipment program at the workplace that includes: (i) a statement of purpose and responsibilities, (ii) written procedures for selection, use, inspection, cleaning, maintenance and storage of protective equipment, (iii) instruction and training in the correct use and maintenance of the equipment, (iv) medical assessment of respirator wearers, (v) documentation, and (vi) program review; (b) Employer must review PPE program annually in consultation with the workplace JHSC or health and safety representative, as applicable; (c) Annual review must: (i) assess exposure control measures to ensure their continued effectiveness, (ii) determine the need for further control, (iii) ensure the adequacy of instruction, and (iv) assess the adequacy of exposure monitoring data for respirators and assess the need for further monitoring, and ensure the adequacy of the fit test program [OHS Reg, Secs. 8.5 and 8.6]
Equipment: (a) General: Employer must, in consultation with JHSC or safety representative, select an appropriate respirator that: (i) meets CSA Z94.4-93, and (ii) meets the protection factor set out for that particular type of respirator under Table 8-1 of the Regulation based on the maximum use concentration for the contaminant [OHS Reg, Secs. 8.33 and 8.34]; (b) IDLH: Workers required to enter or work in an IDLH or oxygen deficient atmosphere must: (i) wear a full facepiece positive pressure respirator which is either an SCBA, or an airline respirator with an auxiliary self- contained air cylinder of sufficient capacity to permit the worker to escape unassisted from the contaminated area if the air supply fails, and (ii) be attended by at least one other worker stationed at or near the entrance to the contaminated area who is similarly equipped and capable of effecting rescue [OHS Reg, Sec. 8.35]; (c) Emergency escape respirators: If the nature or quantity of an air contaminant and nature of the work area may prevent escape from a contaminated area without help, the worker must have an emergency escape respirator that’s: (i) carried on the worker’s person or within arm’s reach at all times, and (ii) sufficient to allow the worker to leave the contaminated area without help [OHS Reg, Sec. 8.36]; (d) Compressed breathing air: (i) Compressed breathing air supplied for an SCBA and a supplied air respirator must be tested at least annually to ensure that the air meets the requirements of CSA-Z180.1-00, (ii) Air inside an SCBA cylinder that isn’t used for over a year must be slowly depressurized to atmosphere and refilled with compressed breathing air meeting CSA-Z180.1-00 [OHS Reg, Sec. 8.37]
Maintenance: (a) Compressed air cylinders must be inspected in accordance with CSA Z94.4-02; (b) SCBA, including regulators, must be serviced and repaired by qualified persons; (c) Compressed air cylinders must be hydrostatically tested in accordance with CSA-B339-96, Cylinders, Spheres, and Tubes for the Transportation of Dangerous Goods [OHS Reg, Sec. 8.45]
Use: (a) Employer must ensure that respiratory protective equipment is used, stored and maintained in accordance with CSA Z94.4-02; (b) If a worker who wears prescription eyeglasses must wear a full facepiece respirator, the employer must assess the work to be performed, and provide appropriate specialty corrective eyewear if necessary to ensure the work can be performed safely; (c) The employer may allow a worker required to wear a full facepiece respirator use contact lenses if it’s not likely to adversely affect the worker’s health or safety; (d) Nothing is permitted which intrudes between the facepiece and the face, or interferes with the face seal of the facepiece, except for specialty eyewear approved by the Board for use with positive pressure full facepiece respirators; (e) A worker required to wear a respirator which requires an effective seal with the face must be clean shaven where the respirator seals with the face; (f) Workers must perform a positive or negative pressure user seal check in accordance with CSA-Z94.4-02 each time before they use a respirator requiring an effective seal with the face for proper functioning (other than before using an escape respirator in an emergency) [OHS Reg, Secs. 8.38, 8.39 and 8.41]
Fit Test: (a) A respirator requiring an effective seal with the face may not be issued to a worker unless a fit test demonstrates that the facepiece forms an effective seal with the wearer’s face; (b) Fit tests must be performed in accordance CSA Z94.4-02; (c) A fit test must be carried out: (i) before initial use of a respirator, (ii) at least once a year, (iii) whenever there’s a change in respirator facepiece, including the brand, model, and size, and (iv) whenever changes to the user’s physical condition could affect the respirator fit; (d) Workers must wear whatever other PPE they have to wear at the same time as the respirator during a fit test [OHS Reg, Sec. 8.40]
Medical Assessment: If there’s any doubt about the worker’s ability to use a required respirator for medical reasons, the worker must be examined by a physician who gets sufficient information to advise the employer about the worker’s ability to wear a respirator. [OHS Reg, Sec. 8.42]
Training: Employer must ensure that any worker who wears PPE is adequately instructed in the correct use, limitations and assigned maintenance duties for the equipment [OHS Reg, Sec. 8.7]
Records: Employer must maintain a record of: (a) Fit test results; (b) Instructions to workers; (c) Maintenance for air supplying respirators, powered air purifying respirators, and sorbent cartridges and canisters; and (d) Maintenance and repairs for each self-contained breathing apparatus and all air cylinders in accordance with CSA Z94.4-02 [OHS Reg, Sec. 8.44]
MANITOBA
Code of Practice/Program: Not specifically required
Equipment: (a) General: Employer must ensure that respiratory protective equipment provided to a worker is selected, used and maintained in accordance with CSA Z94.4-11; (b) Atmosphere-supplying: Employer must ensure that air in an atmosphere-supplying respirator provided to a worker meets the purity requirements of CSA Z180.1-13; (c) IDLH: Employer must provide worker who’s required to enter an IDLH atmosphere one of the following atmosphere-supplying respirators: (i) an open-circuit SCBA, which (x) is sufficiently charged to enable the worker to perform the work safely, (y) operates in a pressure demand or positive pressure mode, and (z) has a minimum rated capacity of 30 minutes, (ii) an airline respirator equipped with a full face piece that (x) operates in a pressure demand or positive pressure mode, and (y) has an auxiliary supply of air that’s carried on the person or within arm’s reach and sufficient to allow the worker to escape if the primary air supply equipment fails, or (iii) a closed-circuit SCBA [WSH Regs, Secs. 6.15 and 6.16]
Use: Employer must: (a) Develop and implement safe work procedures for the use of PPE in the workplace; (b) Ensure those safe work procedures aren’t inconsistent those established by the PPE’s manufacturer; (c) Train and ensure workers comply with the safe work procedures; (d) Ensure that workers comply with those safe work procedures; and (e) Ensure the equipment provided fits the worker correctly and can be safely used by the worker [WSH Regs, Secs. 6.2 and 6.4]
Maintenance and Storage: Employer must: (a) Ensure that the equipment is: (i) stored in a location that’s clean, secure, and readily accessible by the worker, (ii) immediately repaired or replaced if it’s defective, and (iii) immediately replaced with clean or decontaminated equipment if it’s rendered ineffective because of contamination with a hazardous substance; and (b) Make, so far as is reasonably practicable, appropriate adjustments to the work procedures and rate of work to eliminate or reduce any risk to the safety or health of a worker that may arise from the worker’s use of the equipment [WSH Regs, Sec. 6.3]
Training: Employer must ensure that a worker using respiratory protective equipment: (a) Is adequately trained by a competent person in the proper fit, testing, maintenance, use and cleaning of the equipment and in its limitations; (b) Is able to test, maintain and clean the equipment; (c) Is able to use the equipment safely; and (d) Inspects and tests the equipment before each use [WSH Regs, Sec. 6.15]
NEW BRUNSWICK
Code of Practice/Program: If an employer is required to provide respiratory protective equipment, it must: (a) In consultation with the JHSC or health and safety representative, establish a written code of practice covering the proper selection, care, use, maintenance and fitting of the equipment; (b) Ensure the code of practice complies with CSA Z94.4-93; and (c) Ensure that a copy of the code of practice is readily available to an OHS officer upon request and to employees in the areas where the respiratory protective equipment may be required [OHS General Reg, Sec. 45]
Equipment: (a) General: Respiratory protective equipment must meet the requirements of CSA Z94.4-93; (b) Firefighter: A firefighter who may be exposed to an oxygen deficient atmosphere or harmful concentrations of air contaminants when engaged in structural fire-fighting or rescue must wear positive-pressure self-contained respiratory protective equipment that meets or exceeds NFPA 1981, 1992 edition, together with a protective hood that meets or exceeds the requirements in Chapter 6-1 of NFPA 1971, 1991 edition; (c) SCBA: Employer must ensure that the compressed breathing air used in self-contained respiratory protective equipment required under subsection (b) meets or exceeds CSA Z180.1-M85; (d) Structural firefighting: Employer must ensure that self-contained respiratory protective equipment used by a firefighter engaged in structural fire-fighting or rescue is equipped with a personal distress alarm device that meets or exceeds NFPA 1982, 1993 edition [OHS General Reg, Sec. 51.6]
Use and Maintenance: (a) Employer must ensure that required respiratory protective equipment is properly used, maintained, inspected and stored in accordance with CSA Z94.4-93; (b) An employee who may be required to use respiratory protective equipment must co-operate in attaining an effective fit of the equipment and be as clean shaven as necessary to ensure an effective facial seal. [OHS General Reg, Secs. 45 and 47]
Training: Employer must: (a) Ensure that the employee is instructed and trained in the proper use and care of the protective equipment; (b) Implement a training program for an employee who may have to use, issue, test or maintain respiratory protective equipment or supervise an employee who may have to use respiratory protective equipment; and (c) Use clause 8 of CSA standard Z94.4-93 as a guide to the necessary content of the training program required [OHS General Reg, Secs. 38 and 46]
NEWFOUNDLAND
Code of Practice/Program: Employer must establish, implement and maintain, and revise where necessary, a written respiratory protection program in accordance with CSA Z94.4 [OHS Regs, Sec. 83]
Equipment: Employer must: (a) General: Select and provide appropriate respiratory protection equipment certified by NIOSH based on the respiratory hazard to which a worker is exposed and workplace and user factors that affect the equipment’s performance and reliability; (b) Compressed air: Ensure that compressed air, compressed oxygen, liquid air and liquid oxygen used for respiration comply with CSA Z180.1 [OHS Regs, Secs. 84 and 85]
Use: (a) Respiratory equipment must be used in compliance with the conditions of its certification; (b) Employer must not allow a respirator with a tight-fitting facepiece to be worn by an employee who has: (i) hair on the face or scalp that is likely to prevent effective sealing of the facepiece to the facial skin; o (ii) a condition that interferes with the face to facepiece seal or valve function; (c) If an employee wears corrective glasses or goggles or other personal protective equipment, the employer must ensure that the equipment is worn in a manner that doesn’t interfere with the seal of the facepiece to the user’s face; (d) If a tight-fitting respirator is used, employer must ensure that the employee performs a user seal check before each use [OHS Regs, Sec. 85]
Maintenance and Inspection: (a) Respiratory protection equipment issued for the exclusive use of an employee must be cleaned and disinfected as often as necessary to keep it in sanitary condition; (b) Respiratory protection equipment issued for the use of more than one employee must be cleaned and disinfected before being worn by different individuals; (c) Employer must ensure that: (i) respiratory protection equipment used in routine situations is inspected before each use and after cleaning, (ii) respiratory protection equipment maintained for use in emergency situations is inspected at least once monthly and according to the manufacturer’s recommendations, and is checked for proper function before and after each use, and (iii) emergency escape only equipment is inspected before being carried into the workplace for use; (d) Equipment must be discarded when the above inspections find damage [OHS Regs, Sec. 86]
Training: Employer must ensure that a worker who wears PPE is adequately instructed in the correct use, limitations and assigned maintenance duties for the equipment [OHS Regs, Sec. 72]
NOVA SCOTIA
Code of Practice/Program: Not specifically required
Equipment: (a) General: Respiratory protective equipment must meet the requirements of CSA Z94.4; (b) Compressed breathing air: Employer must ensure that the compressed breathing air in a respirator meets or exceeds the latest version of CSA Z180.1, (c) Firefighter: A firefighter who may be exposed to an oxygen deficient atmosphere or harmful concentrations of air contaminants when engaged in structural fire-fighting must wear positive-pressure self-contained respiratory protective equipment that meets or exceeds the latest version of NFPA 1981, together with a protective hood that meets or exceeds the requirements in the latest version of NFPA 1971; (c) Structural firefighting: Employer must ensure that self-contained respiratory protective equipment used by a firefighter engaged in structural fire-fighting is equipped with a personal distress alarm device that meets or exceeds the latest version of NFPA 1982 [Occ Safety General Regs, Secs. 13 and 195]
Use and Maintenance: Employer must ensure that: (a) An employee wears or uses PPE in accordance with the instruction and training provided; (b) All required PPE is maintained by a competent person and tested or visually inspected before each use, in accordance with the manufacturer’s specifications; (c) PPE identified as having any defect that may impair its adequacy of the equipment isn’t used until it’s repaired [Occ Safety General Regs, Sec. 9]
Training: Employee must ensure that employee receives adequate training in the proper use and care of PPE he/she is required to use [Occ Safety General Regs, Sec. 9]
Fit Testing: Employer must ensure that firefighters receive annual quantitative fit testing of their self-contained respiratory protective equipment [Occ Safety General Regs, Sec. 196]
ONTARIO
Code of Practice/Program: An employer who provides a worker with a respirator must establish written measures and procedures regarding the selection, care and use of respirators [R.R.O. 1990, Reg 833, Control of Exposure to Biological or Chemical Agents, Sec. 9(2)]
Equipment: (a) General: Respirator must: (i) be approved by either: (x) NIOSH, or (y) a testing and certification agency other than NIOSH and, in the opinion of a person qualified because of knowledge, training and experience in industrial hygiene practice, afford the worker protection at least equal to the protection of a NIOSH approved respirator approved by NIOSH, and (ii) meet or exceed the applicable assigned protection factor set out in Schedule 2 of the Regulation for the particular equipment; (b) Asbestos: A respirator used to protect from exposure to asbestos, it must be equipped with either: (i) a HEPA filter, or a N-100, R-100 or P-100 particulate filter; (c) IDLH: An airline respirator used in an IDLH atmosphere must be fitted with an auxiliary supply of breathing air sufficient to permit the worker to escape unassisted from the atmosphere; (d) Supplied air: A respirator supplied with breathing air from an air cylinder or compressed breathing air system must meet the following requirements: (i) the breathing air must meet the purity requirements in Table 1 of CSA Z180.1-13 (R2018), (ii) if a compressed breathing air system uses a compressor with an operating pressure greater than 103.4 kPa to supply the breathing air, the breathing air must be tested at least once every 6 months to ensure that it meets the above requirement, (iii) the air intake used in connection with a compressed breathing air system must: (x) for breathing air delivered by a compressor with an operating pressure greater than 103.4 kPa, be located in accordance with section 6 (Air intakes) and Annex A of CSA Z180.1-13 (R2018), and (y) for breathing air delivered by an ambient air system, be located in accordance with section 6 (Air intakes) and Annex B of CSA Z180.1-13 (R2018), (iv) if a compressed breathing air system uses an oil-lubricated compressor to supply the breathing air (x) a continuous carbon monoxide monitor equipped with audible and visual alarms that activate at 5 ppm must be provided, and (y) the continuous carbon monoxide monitor must be calibrated in accordance with the manufacturer’s instructions [R.R.O. 1990, Reg 833, Control of Exposure to Biological or Chemical Agents, Sec. 10]
Use: (a) A respirator must be used in accordance with the manufacturer’s instructions; (b) A worker may not be assigned to an operation that requires the use of a respirator unless he/she is physically able to perform the operation while using the respirator; (c) A worker must conduct positive and negative pressure user seal checks before every use of a tight-fitting elastomeric respirator; and (d) A respirator designed to be tight-fitting may not be provided to, or used by, a worker with facial hair that comes between the sealing surface of the facepiece and the face or that interferes with the functioning of the respirator [R.R.O. 1990, Reg 833, Control of Exposure to Biological or Chemical Agents, Secs. 11 and 12]
Maintenance: Respirator must be cared for and maintained in accordance with the manufacturer’s instructions [R.R.O. 1990, Reg 833, Control of Exposure to Biological or Chemical Agents, Sec. 13]
Fit Test: (a) A respirator designed to be tight-fitting must be tested for fit via either a qualitative or quantitative fit test [R.R.O. 1990, Reg 833, Control of Exposure to Biological or Chemical Agents, Sec. 12]
Training: (a) An employer who provides a worker with a respirator must provide training and instruction in the care and use of the respirator before the worker first uses the respirator; and (b) Training and instruction must cover: (i) the respirator’s limitations, (ii) inspection and maintenance of the respirator, including, in the case of an air-purifying respirator, end of service life indicators or change out schedules for the cartridge, canister or filter, (iii) proper fitting of the respirator, and (iv) cleaning and disinfecting the respirator [R.R.O. 1990, Reg 833, Control of Exposure to Biological or Chemical Agents, Sec. 9]
PRINCE EDWARD ISLAND
Code of Practice or Program: Not specifically required
Equipment: (a) General: Respirators must meet CSA Z94.4-18; (b) Supplied air: Employer must ensure that air provided for the purpose of any respiratory protective equipment meets the applicable standards and specifications set out in CSA Z180.1-19; (c) IDLH: The employer must ensure that if a worker is wearing an approved air-line or approved air-hose type respirator in an atmosphere immediately harmful to the worker: (i) the air supply source is attended by another worker equipped to effect rescue or render assistance, and (ii) the worker is provided with and carries an auxiliary supply of compressed respirable air of sufficient capacity to enable escape from the area in an emergency or until rescue [OHS Act General Regs, Secs. 45.18 and 45.20]
Use and Maintenance: Employer must ensure that: (a) Selection, use and care of respirators meet CSA Z94.4-18; (b) Workers required to use a respirator are clean shaven where the respirator seals with the face; (c) Workers wearing or using PPE test the equipment before each use and don’t wear or use any equipment they have reason to believe is defective [OHS Act General Regs, Secs. 45.18, 45.19 and 45.3]
Training: Employer must ensure that that every worker required to use PPE gets pre-job instruction by the employer to understand its use, limitations, and maintenance requirements [OHS Act General Regs, Sec. 45.3]
QUÉBEC
Code of Practice/Program: Employer must draft and implement a respiratory protection program that meets CSA Z94.4-93 [OHS Reg, Sec. 45]
Equipment: (a) General: Respirators must be designed to offer protection from the danger to which the worker’s exposed and meet CSA Z94.4-93; (b) Supplied air: (i) compressed breathing air for supplied-air respirators or self-contained respiratory protective apparatuses must meet CSA Z180.1-00, (ii) systems that produce, store and distribute air must meet the standard that applies to them, (iii) samples of compressed breathing air must be taken and analyzed to obtain an accuracy equivalent to that obtained by applying the methods described in the Sampling Guide for Air Contaminants published by the Institut de recherche Robert-Sauvé en santé et sécurité du travail du Québec, (iv) the analyses must be made at least every 6 months, except for ambient air systems, (v) breathable compressed air supply and distribution systems must be maintained in compliance with the manufacturers’ instructions, (vi) employer may not provide worker a self-contained or air-supplied protective respiratory apparatus equipped with an automatic device which interrupts or restricts the air supply in the part of the apparatus covering the face [OHS Reg, Secs. 45 and 48]
Use and Maintenance: Required respiratory protective equipment must be: (a) Used in accordance with CSA Z94.4-93; (b) Kept in good working order; (c) Inspected by workers each time they wear it; (d) Inspected by the employer at least once a month and each time the worker using the equipment reports to the employer that it’s not working properly; (e) Disinfected before being used by another worker, except in an emergency; and (f) Stored in a clean place [OHS Reg, Sec. 47]
Training: Employer must ensure that principles of operation and use of the equipment are explained to and fully understood by the workers [OHS Reg, Sec. 47]
Records: (a) Results of the air sample analyses required every 6 months must be entered in a register that must be kept for a period of at least 5 years; (b) Breathable compressed air supply and distribution systems must be maintained in compliance with the manufacturers’ instructions and employer must record date on which maintenance is performed and who performed it in a register kept for at least 5 years [OHS Reg, Sec. 48]
SASKATCHEWAN
Code of Practice or Program: Not specifically required
Equipment: (a) General: Respiratory protective device must be “approved” and: (i) provide suitable and adequate protection to the worker from one or more airborne contaminants, (ii) be of the proper size for the worker’s face, and (iii) if where a tight fit is essential to proper functioning, make an effective seal to the worker’s facial skin [OHS Regs, Secs. 88(1)]; (b) Supplied air: Employer must ensure that compressed air in an atmosphere-supplying respirator used by a worker in an IDLH atmosphere meets the purity requirements in Table 2 of CSA Z180.1-M85 [OHS Regs, 90(3)]; (c) IDLH: Employer must ensure that worker required to enter IDLH atmosphere is provided and uses an approved atmosphere-supplying respirator that is: (i) an open-circuit SCBA that: (w) operates in a pressure demand or other positive pressure mode, (x) has a minimum rated capacity of 30 minutes, (y) is sufficiently charged to enable the worker to perform the work safely, and (z) is equipped with a low-pressure warning device or an escape respirator; (ii) an airline respirator equipped with a full facepiece that: (x) operates in a pressure demand or other positive pressure mode; and (y) has an auxiliary supply of air sufficient to allow the worker to escape in case of failure of the primary air supply equipment; or (iii) a closed-circuit SCBA [OHS Regs, 90(1)]
Maintenance and Inspection: Employer must ensure that the respiratory protective device is: (a) Regularly cleaned and maintained in an approved manner; (b) Kept, when not in use, in a convenient and sanitary location in which the respiratory protective device is not exposed to extremes of temperature or to any contaminant that may inactivate it; (c) If it’s used for emergency use, thoroughly inspected by a competent person at least once a month and after each use [OHS Regs, Secs. 88(1) and 89]
Fit Test: If a tight fit is essential to ensure worker isn’t exposed to airborne contaminant(s) that may pose a risk of significant harm, employer must ensure the respiratory protective device has been fit-tested by a competent person in an approved manner [OHS Regs, 88(1)]
Training: If a required respiratory protective device is provided to a worker, employer must ensure that: (a) The worker is trained by a competent person in the proper testing, maintenance, use and cleaning of the device and its limitations; (b) The worker can demonstrate that he/she: (i) understands the training provided, (ii) can test, maintain and clean the respiratory protective device, and (iii) can use the respiratory protective device safely; (c) The worker tests the respiratory protective device before each use; (d) The worker is assessed according to an approved standard as being capable of wearing a respiratory protective device and adequately informed of the reasons for the assessment; (e) The required training includes practical experience by the worker in an uncontaminated environment; and (f) The worker given semi-annual refresher training in the device’s safe use if the device is used only for emergency purposes [OHS Regs, Secs. 88(2) to (4)]
Records: Employer must ensure that: (a) The following records are kept as long as the worker is employed by the employer and made readily available for inspection and examination by the JHSC or health and safety representative: (i) records of fit-testing for each worker, (ii) records of the results of assessments of each worker’s capability of wearing a respiratory protective device, (iii) records of the training completed by each worker, (iv) records of monthly inspections of respiratory protective devices used for emergency use listing the name of the inspector which must be conspicuously displayed at the location where the device is stored; (b) Records respecting a worker that are made available for inspection and examination don’t disclose any personal health information about the worker, unless the worker agrees to that disclosure; (c) Records of the maintenance of atmosphere-supplying respirators are kept and made readily available for inspection and examination by the JHSC or safety representative as long as that worker is employed by the employer; and (d) A worker is allowed to inspect records pertaining to him/her at any time [OHS Regs, Secs. 88(5) to (8) and 89]
NORTHWEST TERRITORIES & NUNAVUT
Code of Practice or Program: Not specifically required
Equipment: (a) General: Respiratory protective device must be “approved” and: (i) provide suitable and adequate protection to the worker from one or more airborne contaminants, (ii) be of the proper size for the worker’s face, and (iii) if where a tight fit is essential to proper functioning, make an effective seal to the worker’s facial skin [OHS Regs, Sec. 92(1)]; (b) Supplied air: Employer must ensure that compressed air in an atmosphere-supplying respirator used by a worker in an IDLH atmosphere meets approved purity requirements [OHS Regs, 92(4)]; (c) IDLH: Employer must ensure that worker required or allowed to enter IDLH atmosphere is provided and uses an approved atmosphere-supplying respirator that is: (i) an open-circuit SCBA that: (w) operates in a pressure demand or other positive pressure mode, (x) has a minimum rated capacity of 30 minutes, (y) is sufficiently charged to enable the worker to perform the work safely, and (z) is equipped with a low-pressure warning device or an escape respirator; (ii) an airline respirator equipped with a full facepiece that: (x) operates in a pressure demand or other positive pressure mode; and (y) has an auxiliary supply of air sufficient to allow the worker to escape in case of failure of the primary air supply equipment; or (iii) a closed-circuit SCBA [OHS Regs, 92(2)]
Maintenance and Inspection: Employer must ensure that the respiratory protective device is: (a) Regularly cleaned and maintained in an approved manner; (b) Kept, when not in use, in a convenient and sanitary location in which the respiratory protective device is not exposed to extremes of temperature or to any contaminant that may inactivate it; (c) If it’s used for emergency use, thoroughly inspected by a competent person at least once a month and after each use [OHS Regs, Secs. 91(1) and 92]
Fit Test: If a tight fit is essential to ensure worker isn’t exposed to airborne contaminant(s) that may pose a risk of significant harm, employer must ensure the respiratory protective device has been fit-tested by a competent person in an approved manner [OHS Regs, 91(1)]
Training: If a required respiratory protective device is provided to a worker, employer must ensure that: (a) The worker is trained by a competent person in the proper testing, maintenance, use and cleaning of the device and its limitations; (b) The worker can demonstrate that he/she: (i) understands the training provided, (ii) can test, maintain and clean the respiratory protective device, and (iii) can use the respiratory protective device safely; (c) The worker tests the respiratory protective device before each use; (d) The worker is assessed according to an approved standard as being capable of wearing a respiratory protective device and adequately informed of the reasons for the assessment; (e) The required training includes practical experience by the worker in an uncontaminated environment; and (f) The worker gets semi-annual refresher training in the device’s safe use if the device is used only for emergency purposes [OHS Regs, Secs. 91(2) to (4)]
Records: Employer must ensure that: (a) The following records are kept as long as the worker is employed by the employer and made readily available for inspection and examination by the JHSC or health and safety representative: (i) records of fit-testing for each worker, (ii) records of the results of assessments of each worker’s capability of wearing a respiratory protective device, (iii) records of the training completed by each worker, (iv) records of monthly inspections of respiratory protective devices used for emergency use listing the name of the inspector which must be conspicuously displayed at the location where the device is stored; (b) Records of the maintenance of atmosphere-supplying respirators are kept and made readily available for inspection and examination by the JHSC or safety representative as long as that worker is employed by the employer; and (c) A worker is allowed to inspect records pertaining to him/her at any time [OHS Regs, Secs. 91(5) to (7) and 92]
YUKON
Code of Practice or Program: Not specifically required
Equipment: (a) General: Respiratory protective equipment must be selected in accordance with CSA Z94.4-02 or other similar standard acceptable to the Director [OHS Regs, Sec. 1.27]; (b) Supplied air: Compressed air supplied to respirators, such as SCBA or ‘supplied quality respirators’, must be tested at least annually to check the quality of the air and compliance with CSA Z180.1-00, or other similar standard acceptable to the Director [OHS Regs, Sec. 1.30]; (c) IDLH: If a worker is required to work in an IDLH or oxygen deficient atmosphere, or there’s risk of accidental release of an air contaminant or atmosphere development of such conditions, employer must provide and worker must wear a full facepiece positive pressure respirator that’s an SCBA, or an airline respirator with sufficient capacity to permit the worker to escape from the contaminated area without help if air supply fails; worker using SCBA or an airline respirator when there’s any possibility that the worker may not receive assistance must carry or ensure that an emergency escape air bottle is within arm’s reach at all times [OHS Regs, Secs. 1.28 and 1.29]
Use: (a) When a worker uses a positive pressure full facepiece respirator, nothing can interfere with the face seal of the facepiece except for specialty eyewear approved by the respirator’s manufacturer or Director for use with positive pressure full facepiece respirators; (b) Contact lenses are OK if they don’t endanger worker’s health and safety; and (c) A worker required to wear a respirator that requires an effective seal with the face for proper functioning must be clean-shaven where the respirator seals with the face [OHS Regs, Secs. 1.31 and 1.32]
Fit Test: Fit tests and fit checks must be done on workers as required to ensure an acceptable performance from respirators being used [OHS Regs, Sec. 1.33]
Training: Worker must be adequately trained in respiratory protective equipment’s use, limitations and maintenance [OHS Regs, Sec. 1.27]
Records: Employer must keep records of fit tests performed on workers [OHS Regs, Sec. 1.33]
Leave A Comment