Best Practices for Working Safely with Adhesives & Resins
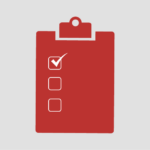
Many industries use chemical substances known as adhesives and resins to join surfaces and materials during the product assembly and construction process. Adhesives may be in the form of an aerosol that’s applied by spraying or a liquid applied by spraying, rolling, or dipping. While vital to the product assembly and construction process, industrial adhesives can cause respiratory problems, fire, explosion, eye injury, and other hazards if they’re not used properly. Here’s a Checklist of Best Practices to ensure the safe and legally compliant handling, storage, and disposal of adhesives and resins.
Adhesives & Resins Hazard Assessment & General Controls
Verify that:
A competent person(s) has performed a hazard assessment of all potentially hazardous adhesives and resins used and stored at the work site.
Measures are in place to keep workers’ exposure to hazardous vapours at or below the permissible exposure limit (PEL) for the particular substance under OHS regulations.
Measures to ensure the safe use, handling, storage, cleanup, and disposal of storage of adhesives and resins comply with the applicable product’s SDS safety information and manufacturer’s instructions as well as OHS requirements.
Hazard controls are regularly monitored.
The hazard assessment is reviewed and, if necessary, updated at least once a year and in response to adhesives injuries or incidents, the introduction of new products and other indications that the current assessment may be outdated.
Adhesives & Resins WHMIS Measures
Verify that:
An up-to-date and compliant Safety Data Sheet (SDS) is kept for each adhesive and resin product used or stored at the site.
SDS’ are kept in a central location at the site that’s readily available and known to all workers that use or handle adhesives and resins.
All adhesive and resin product containers are properly labeled in accordance with WHMIS requirements.
All exposed workers receive WHMIS training covering the specific hazards of adhesives and resins and how to access and read an SDS and use the safety information it lists to protect themselves.
WHMIS training is reviewed at least once a year.
Exposed workers receive revised or renewed WHMIS training as often as necessary to ensure their safety.
Engineering Controls for Adhesives & Resins
Verify that reasonably practicable engineering controls to protect exposed workers are in place in work areas where adhesives and resins are used, stored and disposed of, which may include:
General ventilation to ensure adequate airflow and dilute and remove hazardous vapours and airborne contaminants.
Exhaust fans, open windows, or other local ventilation to improve air circulation.
Hoods or other devices to capture and remove contaminants at the source of the emission, such as where adhesives are being dispensed or mixed.
Enclosures and physical barriers to minimize workers’ exposure.
Automated equipment or remotely controlled systems to perform adhesives handling tasks, eliminating the need for workers to be exposed.
Work/Administrative Controls for Adhesives & Resins
Verify that work or administrative controls are in place to minimize the hazards posed by adhesives and resins handling, storage, and disposal operations, which should include:
Replacing hazardous adhesives and resins with less toxic or flammable alternatives, whenever reasonably practicable.
Carrying out all adhesives and resins operations in accordance with the safety information listed in the SDS and manufacturers’ instructions.
Creating, implementing, and training workers in safe work procedures for hazardous adhesives and resins operations.
Use of adhesives that require lower temperatures for application to reduce the risk of burns and exposure to hot vapours.
Requiring workers to use proper grounding and bonding procedures when dispensing flammable adhesives and resins.
Implementing policies and procedures to prevent potential sources of ignition in operations involving flammable adhesives and resins, including but not limited to banning workers from smoking or using tools or equipment that may generate sparks and steps to prevent the accumulation of static electricity.
PPE for Adhesives & Resins
Verify that:
PPE is not the primary means of protecting workers but used only as a safety measure of last resort when adhesives and resins hazards can’t be totally eliminated by substitution or engineering controls.
PPE used is selected based on the PPE recommended in the SDS for the particular product.
PPE is used, cleaned, stored, and maintained in accordance with the PPE product’s manufacturer’s instructions.
All PPE (and, in the case of respirators, component parts) meet the standards required by provincial OHS laws for that particular piece of equipment.
Where required by OHS laws, the company provides the PPE workers are required to use at no cost to the workers.
All workers receive safety training in the use of each kind of PPE they’re required to use.
Workers who work with or near adhesives or resins that emit toxic fumes are provided and use appropriate respiratory protective equipment.
Workers who use respirators are medically evaluated and fit tested where required by OHS regulations.
Workers wear chemical-resistant and/or burn-resistant gloves to protect their hands from direct contact with the adhesive or resin.
Workers exposed to risk of chemical splashes or burns use safety glasses, goggles, face shields, or equivalent PPE to protect their eyes and face.
Workers that handle hot melt or flammable adhesives wear heat-resistant clothing, coveralls, aprons, or other equivalent skin and body protection.
Where required by OHS regulations, there are suitable emergency showers and eye wash stations at sites where adhesives and resins are handled or stored.
Safe Storage of Adhesives & Resins
Verify that:
All adhesives and resins are stored in approved containers and areas.
Containers are kept closed when not in use.
Only closed containers are used for transport or storage.
Incompatible chemical products that may cause a hazardous reaction if they come into contact with each other aren’t stored together.
Smoking, sparking tools, and other sources of ignition are banned in in flammable liquid storage areas.
Liquid adhesives and resins are stored in a cool, dry place away from heat and direct sunlight.
Indoor storage areas for flammable liquids are adequately ventilated.
There are suitable and readily available fire extinguishers in all areas where flammable liquid adhesives and resins are stored, transported, or used.
Flammable liquids aren’t carried with explosives in vehicle cargo space.
Safe Disposal of Adhesives & Resins
Verify that:
There are procedures, materials, and equipment in place to ensure the safe disposal of adhesives and resins and product containers.
There are procedures, materials, and equipment in place to ensure the safe cleanup of leaks and spills.
The above disposal and cleanup procedures comply with the safety information listed on the product’s SDS and the manufacturer’s instructions.