The Insider’s 10th Annual Due Diligence Scorecard, Part 2: 20 Lessons from Recent Due Diligence Cases
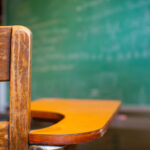
Part 1 of the Insider’s 10th annual Due Diligence Scorecard included 21 safety prosecutions decided since Sept. 2013 in which the verdict turned on the success or failure of a company’s or individual’s due diligence defence. These court and tribunal decisions aren’t of use only to lawyers—they also provide concrete examples for safety professionals of steps defendants took that successfully supported their due diligence defences and errors that cost them this defence. Here in Part 2 of the Scorecard, we’ve extracted 20 lessons that you can learn from these cases and apply to your own OHS program. (See the box at the end for a review of six key facts about the due diligence defence.)
20 KEY DUE DILIGENCE LESSONS
[learn_more caption=”Lesson #1: Use Near Misses to Prevent Actual Incidents”]
The response to a near miss in the workplace shouldn’t be just a sigh of relief that no one was hurt or killed. Near misses should be seen as opportunities. They reveal hazards that you can then address by implementing appropriate safety measures. Thus, near misses put employers on notice that something in the workplace is endangering workers. If employers ignore the warnings provided by near misses, they won’t be able to prove due diligence—especially if the hazards involved in prior near misses result in an actual safety incident.
Example: A new and young worker was working as a traffic control person at a road construction site when she was hit from behind by a vehicle and suffered life-threatening injuries. Her employer was issued an administrative penalty for various OHS violations.
The BC Workers’ Compensation Appeals Tribunal was critical of various aspects of the employer’s safety measures at this site but especially its lack of an appropriate response to several previous near misses in which traffic control persons were nearly hit by oncoming vehicles. The employer was aware of these near misses but neither properly investigated them nor implemented appropriate corrective measures in response to them. For example, the Tribunal concluded that the employer didn’t pursue with the municipality a speed reduction for the area of the work. It also failed to adjust the workers’ start times so that the rising sun didn’t blind oncoming drivers and prevent them from seeing the traffic control persons [WCAT-2013-03550].
Insider Says: For more on near misses, see “OHS Program: Answers to 8 FAQs about Near Misses.”
[/learn_more]
[learn_more caption=”Lesson #2: You Must Address Known Safety Hazards”]
A basic rule of due diligence: Once you’re notified or become aware of a safety hazard—or potential hazard—in your workplace or impacting your workers, you must assess the hazard and, if necessary, take all reasonable steps to address it.
Example #1: A driver for a wood shavings company was found buried underneath wood shavings that had emptied from a silo into a truck. The court convicted his employer, rejecting its due diligence defence. When material in the silo clogged, the standard procedure was for workers to stand inside the truck box and poke at the material until it started to fall. But the employer knew this procedure was inherently unsafe. And the hazard it posed was “eminently foreseeable,” said the court. Yet the employer’s safety manual didn’t warn workers of the danger posed by the falling material or tell them to stay away from the silo opening during the procedure. Thus, the court concluded that employer’s procedure didn’t “pass the test of every precaution reasonable in the circumstances” [Reliable Wood].
Example #2: A worker at a home construction site was injured when part of the bank of an excavation collapsed. The general contractor for the project had been warned that this slope was unstable. But the BC Workers’ Compensation Appeals Tribunal found that it didn’t take adequate steps to address this known hazard and ensure the safety of workers at the jobsite. For example, it relied on a plan from an engineer that was merely a proposal and not finalized or certified. It also failed to take other reasonable steps, such as developing a safe work procedure for the work in the excavation, ensuring that the engineer was present during the excavation work and having a professional with geotechnical knowledge determine that the excavation was safe for worker entry [WCAT-2013-02380].
[/learn_more]
[learn_more caption=”Lesson #3: Safety Inspections Should Cover Key Equipment”]
Due diligence requires you to address safety hazards you know or should know about, considering whether a reasonable person would’ve been aware of such hazards. So you must be proactive and take steps to identify actual or potential hazards in the workplace. One important tool for identifying hazards is the health and safety inspection. But such inspections are effective only when they cover all key areas of the workplace and key pieces of equipment—especially those that pose safety risks. (Here are five tips for making your safety inspections more effective.) Failing to inspect such dangerous equipment may mean that hazards get overlooked and unaddressed, which will undermine your due diligence defence.
Example: A warehouse worker’s hair got caught in an unguarded drive shaft under a moving conveyor belt, pulling out her hair and injuring her hand. The employer was convicted of two OHS violations. The court explained that due diligence required the employer to take all reasonably practical steps to ensure the health and safety of workers and address foreseeable hazards. It was reasonably foreseeable that the unguarded drive shaft on the conveyor posed a safety hazard, said the court. But the employer didn’t take reasonable steps to protect workers from this hazard.
For example, the employer had a JHSC, which used a six-page checklist to conduct safety inspections of the warehouse. But the checklist didn’t contain any specific references to conveyors by name or by individual conveyor, noted the court. And the JHSC inspectors weren’t trained or expected to look closely at conveyors—despite the fact that conveyors were a crucial piece of equipment in the warehouse and posed serious safety hazards to workers. In short, the employer relied upon its JHSC to spot the lack of guarding on conveyors when its members were doing inspections but no one bothered to look closely at this equipment during those inspections, concluded the court [Value Drug].
[/learn_more]
[learn_more caption=”Lesson #4: Having a Good General OHS Program Isn’t Enough”]
It’s essential to have an OHS program—that is, a formal system that spells out general safety rules and procedures, and defines the roles and responsibilities of the employer, supervisors and workers within that system. Your OHS program must also have specific safety procedures and rules for the company’s operations, equipment, worksites and the jobs or activities that workers perform. But having a program that’s effective in general won’t support your due diligence defence if the program fails under specific circumstances.
Example #1: A pulp and paper company hired a scaffolding contractor so that repairs could be made to a bridge connecting two buildings. A worker standing on a scaffold platform near the bridge suffered serious injuries when a long piece of aluminum tubing he was holding came into contact with a nearby power line. The company, as prime contractor for the work, was penalized for OHS violations.
The BC Workers’ Compensation Appeals Tribunal noted that in a general sense, the company had an “exemplary approach” to ensuring that contractors operated safely. For example, the company had screened the scaffolding contractor, trained its workers and audited its safety systems. But due diligence isn’t “merely concerned with a general level of conduct.” It’s also concerned with an employer’s specific conduct under specific circumstances. Here, the proximity of the power line to the scaffolding was an obvious hazard, said the Tribunal. In fact, any worker over the height of 4’ 9” standing on the scaffolding platform would’ve been within 10’ of the power line. Thus, the Tribunal concluded that the company’s conduct as to the particular limits of approach issue for this particular project was not up to its “usual high standard” [WCAT-2013-02499].
Example #2: In WCAT-2013-02380, the Tribunal noted that the general contractor had a safety program and even hired an outside safety consultant to conduct safety audits of its worksites. But there was no evidence that the consultant did an audit of the site where this incident occurred or was even aware of this jobsite. The Tribunal concluded that it was apparent that there was a breakdown in the contractor’s safety program when the work started without its safety coordinator knowing about the worksite, without workers getting a site orientation and without a safety plan in place.
[/learn_more]
[learn_more caption=”Lesson #5: Compliance with Industry Standard Isn’t Necessarily Due Diligence”]
It may be reasonable to base your safety rules or procedures on an industry standard or practice. But complying with industry standards may not be enough to prove due diligence. Following such standards may be evidence that you took reasonable steps as to a particular hazard. However, if the industry standard is itself unsafe or has gaps, following it may actually hurt your company’s chances of a successful due diligence defence. (For more, see “Is Following with an Industry Standard the Same Thing as Due Diligence’”)
Example: An oil company took its truck to a tire shop for work, where it was parked and its engine turned off, with the keys left in the ignition. A supervisor started the truck’s engine while a worker was still working on it. When an oil company worker arrived to pick up the truck, he got in it and drove away, running over and killing the tire shop worker who’d gone underneath it to retrieve a jack. Several defendants were charged with and convicted of safety violations.
The court said that an effective lockout policy would include removal and embargo of the ignition key until all work was completed on a vehicle. But leaving the keys in a vehicle’s ignition was “normal practice” in the tire shop. The shop’s safety program and manual were based on those provided by the Tire Industry Association (TIA) and considered by the shop to be “industry standard.” However, the court noted a significant omission in the TIA’s materials—they didn’t address lockout procedures. The purpose of these procedures is to ensure that a vehicle can’t unexpectedly be energized or moved while a worker is working on it. And the most likely way for that to happen is for someone to turn on the ignition, said the court. So it concluded that leaving the keys in the ignition wasn’t sufficient from a safety perspective [Yukon Tire].
[/learn_more]
[learn_more caption=”Lesson #6: Safety Rules Should Address Specific Hazards & Equipment”]
An effective OHS program must include safety rules and procedures that reflect the workplace and the work done in it, including the specific equipment used and hazards present. For example, if your workers use power saws, you should have safety rules specifically on the safe use of such saws—not just on power tools in general. Due diligence requires you to make sure that all equipment, especially those that pose safety hazards, are covered by your safety rules and procedures.
Example: A company hired an electrician to assess damage to an electrical cable. The electrician conducted an initial assessment of the damage and then returned a few days later to make the repairs. To access the cable, he climbed a ladder that wasn’t secured or held by anyone. The ladder slipped and he fell, suffering serious injuries. The company and a supervisor were acquitted of various safety violations, so the Crown appealed.
The court upheld the acquittal, finding that the defendants had taken all reasonable steps as to the safe use of ladders:
- The company had safety policies on ladders and provided training on ladder safety;
- The policies and training related specifically to the use of ladders in a variety of situations, including the use of a portable ladder for a job of short duration such as in this incident;
- The safety plan for this specific construction site included a hazard assessment for ladders;
- The ladder in question was maintained in good working condition; and
- The supervisor had instructed the electrician not to use the ladder without someone else holding it and had made a scissor lift available as an alternative to using an unsecured ladder [Flynn].
[/learn_more]
[learn_more caption=”Lesson #7: Safety Rules ≠ Physical Guards”]
As previously noted, safety rules and procedures are the cornerstone of any OHS program. But good rules aren’t always enough—and they aren’t substitutes for physical guards. Safety rules and procedures only work if workers comply with them. And workers are human beings who don’t always follow the rules. The purpose of machine guarding requirements is to protect workers from injury by taking individual discretion, judgment and compliance out of the equation. That is, physical guards and other engineering controls are designed to prevent incidents that occur when workers make mistakes or are careless. So arguing that your safe work procedures were adequate replacements for machine guards required under the OHS laws is unlikely to convince a court that you exercised due diligence.
Example: A ski resort’s “magic carpet,” which carried skiers to the top of the hill, would get covered in ice and go off track as it wrapped around a drum. So the resort developed a written safe work procedure that required workers to open an access panel in the return station and spray the drum with a de-icing product. Workers were instructed not to reach into the return station while the carpet was moving. But while de-icing the drum, a worker did reach his hand in, which got caught and injured. The resort was penalized for various OHS violations and appealed.
The BC Workers’ Compensation Appeals Tribunal found that the resort hadn’t exercised due diligence. It explained, “Guarding is not a tertiary or peripheral feature of the safety landscape but rather one that saves lives and serious injury on a daily basis. Guarding obligations are one of the core aspects of safety in the workplace due to the obviously serious or fatal consequences of failing to follow its requirements.” That’s why the OHS regulations show a preference for physical barriers over less concrete safety measures such as warning signs. So although it was laudable that the resort had developed written safety procedures for de-icing and trained workers on these procedures, they weren’t adequate substitutes for the obvious need for a machine guard. Such a guard was required by the OHS regulations and could’ve been installed with little difficulty or expense, added the Tribunal [WCAT-2014-00128].
[/learn_more]
[learn_more caption=”Lesson #8: You Must Have Written Safety Rules & Procedures”]
Your safety rules and procedures must be in writing. Why’ Because it’s too easy for safety procedures that are passed on verbally to get distorted or misunderstood. And distortions or misunderstandings of safety procedures can have serious—and sometimes fatal—consequences. In contrast, written safety procedures are less likely to be misunderstood. As a result, courts are likely to be very critical of a company whose safety procedures aren’t in writing.
Example: A truck driver was loading an excavator onto a trailer behind a truck when the excavator slipped off the trailer and fell onto its side, injuring the driver. The excavation company was charged with OHS violations.
The court convicted the company, rejecting its due diligence defence. The “rule” was that the company owner was the only one who was supposed to operate the excavator. But that safety rule wasn’t in writing—“everyone just knew” who was to operate the machine. The court said, “There appears to have been a reliance on the belief that, oral instructions having been conveyed, it was therefore presumed that those instructions would be understood and complied with.” But there was no evidence of any steps taken to ensure that anyone working for the company understood these instructions. And it was foreseeable that someone else in the company might take it upon himself, depending on the circumstances, to operate the excavator, especially since the keys were left in it. In short, safety procedures don’t need to be elaborate—but they do need to be in writing, concluded the court [Anray].
[/learn_more]
[learn_more caption=”Lesson #9: Workers Must Be Properly Trained”]
Once you have written safety rules and procedures in place, you must train workers on those rules and procedures as well as on the safe use of the equipment that they operate, including PPE. (See, Training Compliance Centre) And you must ensure that your training is effective and comprehensive or else workers may work unsafely—and your company may be charged with a safety offence.
Example: An employer was penalized for various safety violations after a safety officer saw two workers on the edge of a roof without fall protection. The BC Workers’ Compensation Appeals Tribunal rejected the employer’s due diligence defence. The employer provided some fall protection training. But the Tribunal found that this training clearly wasn’t sufficient. For example, at this site, the safety officer had observed that an anchor wasn’t properly installed, a ladder wasn’t tied off and there were loose ropes and other tripping hazards in the work area [WCAT-2014-00457].
[/learn_more]
[learn_more caption=”Lesson #10: Workers Also Require Proper Supervision”]
Properly training workers doesn’t mean that they’ll always follow safety rules and procedures and comply with the OHS laws. That’s why you need to ensure that you adequately supervise them as well.
Example: After a safety officer saw two workers working at the edge of a roof without proper fall protection, their employer was penalized for several safety violations. The BC Workers’ Compensation Appeals Tribunal rejected the employer’s due diligence defence. The Tribunal explained that it’s part of “the nature of the supervision of workers that they may disagree with and find safety systems inconvenient or unnecessary.” Therefore, it’s the role of supervisors to be vigilant against worker non-compliance. “Due diligence requires active confirmation of appropriate conduct and not merely an assumption that appropriate conduct will take place,” concluded the Tribunal. In this case, the employer didn’t adequately supervise workers to ensure that they wore fall protection as directed, such as by having a supervisor visually confirm their use of appropriate PPE and check on its continued use on a regular basis [WCAT-2013-03580].
[/learn_more]
[learn_more caption=”Lesson #11: Supervisors Also Require Training”]
Workers aren’t the only people in the workplace who need training. The company must train its supervisors, too. If a supervisor isn’t adequately trained and fails to fulfill his safety duties, it’s likely that the company will be held liable for this failure.
Example: A safety officer saw two workers and a supervisor on a steeply sloped roof without any fall protection while distributing materials received by crane. The employer was penalized for a fall protection violation. The BC Workers’ Compensation Appeals Tribunal rejected the employer’s due diligence defence, finding that it didn’t take adequate steps as to its supervisors. The Tribunal explained that part of an employer’s duty to provide adequate supervision was to ensure that those with supervisory duties got the necessary supervisor training and had the attitude necessary to ensure safety in the workplace. It added that the training requirements for a supervisor are more onerous than those for a new worker because the expectations for supervisors are also greater.
Here, the supervisor in question hadn’t received all of his supervisory training before starting work as a supervisor. He also said he wasn’t sure how seriously he took safety and discipline. For example, when the officer asked the supervisor why they weren’t using fall protection, he said he “knew better but the crane was charging by the hour.” And he failed to complete a fall protection plan [WCAT-2014-00331].
[/learn_more]
[learn_more caption=”Lesson #12: Enforcement of Safety Rules Is Critical”]
Even with adequate training and supervision, workers don’t always follow safety rules and procedures. That’s why you must take steps to enforce these rules, such as by disciplining workers who violate them. (See, Discipline & Reprisals Compliance Centre) If you become aware that workers aren’t being compliant and do nothing, don’t expect a court to conclude that you’ve exercised due diligence.
Example #1: A worker and a supervisor were installing roofing material on a roof while wearing fall protection harnesses that weren’t attached to lifelines. Their employer was penalized for a fall protection violation. The BC Workers’ Compensation Appeals Tribunal rejected the employer’s due diligence defence. The worker and supervisor had been properly trained and had the appropriate fall protection equipment. But the employer didn’t adequately enforce its fall protection rules. For example, although the employer claimed to have a “three strikes policy,” it just verbally warned non-compliant workers. It never sent any home for failing to use fall protection or required them to get additional fall protection training. And given this incident and the employer’s prior fall protection violations, it was clear that its system wasn’t motivating workers and supervisors to comply. So the employer should’ve done more to ensure their compliance, such as implementing a zero tolerance policy, specifying clear consequences for non-compliance by both workers and supervisors, and training supervisors on their duty to not only monitor compliance by workers but also model appropriate use of fall protection equipment, concluded the Tribunal [WCAT-2013-03241].
Example #2: In yet another case involving fall protection violations, the BC Workers’ Compensation Appeals Tribunal noted that a company had a disciplinary policy that stated that failing to use fall protection was considered a major infraction and a first offence would result in a verbal warning and being sent home without pay. But it never actually imposed such sanctions when it became aware of such infractions. The employer’s failure to implement the disciplinary policy wasn’t reasonable and was evidence of a lack of due diligence, said the Tribunal [WCAT-2014-00554].
[/learn_more]
[learn_more caption=”Lesson #13: If You Do the Above, You Won’t Be Liable for Acts of Rogue Employee”]
If you properly train and supervise workers and supervisors, and enforce your safety rules, you won’t be held liable if a worker or supervisor goes “rogue” and disregards his training.
Example: A safety officer saw a worker in a road-side excavation with walls that were almost vertical and had no shoring. The excavation also appeared to be more than four feet deep. The employer was penalized for training and supervision violations. The BC Workers’ Compensation Appeals Tribunal ruled that the employer had exercised due diligence. The employer had effectively trained and supervised its workers and the subforeman—even sending them to a safety course on trenching a week before the incident. The employer had taken all reasonable steps to ensure that the subforeman was trained, supervised and knowledgeable, said the Tribunal. And it was the subforeman who erred in failing to recognize that the trench requirements applied to this excavation once it exceeded four feet tall. Describing the subforeman’s failure as “baffling,” the Tribunal concluded that the employer wasn’t liable for his oversight [WCAT-2013-002719].
[/learn_more]
[learn_more caption=”Lesson #14: Context of the Work/Violation Is Important”]
In court decisions involving due diligence, courts will often state that employers have to take all reasonable steps under the circumstances. That is, it’s important to consider the specific context of the work or the safety violations when determining what steps would be reasonable under those particular conditions.
Example #1: As workers for a subcontractor were using a crane to move a platform from one floor to another at a construction site, the crane knocked a piece of cast iron pipe off the floor. It hit and killed a supervisor for a plumbing company who was standing below. The subcontractor pleaded guilty to safety violations. The remaining defendants, including the constructor, went to trial and were acquitted.
In upholding the acquittals, the court explained that to determine whether due diligence was established, it had to first take into account the size and nature of the construction project—not because the safety standards would vary but because the means of meeting those standards would reflect the project’s complexity. At this very large, $96 million project, there were an average of 25 trade subcontractors working onsite at any given time. Thus, the project required careful planning and management. In that context, the court concluded that the constructor had taken sufficient steps to ensure the safety of the work at this project [Bay Grenville]. (Those steps are discussed in more detail in Lesson #16.)
Example #2: In WCAT-2013-002719 discussed above, the Tribunal considered the very large size of the employer, scope of its work throughout the province and hundreds of crews and projects it had going on at any one time. Although the employer had prior safety violations, to merely conclude that it had a “poor safety attitude” as a result was to “ignore the context of the wide array of work and large number of workers operating in this constantly evolving landscape of worker safety,” explained the Tribunal.
[/learn_more]
[learn_more caption=”Lesson #15: Clearly Spell out Safety Duties with Contractors”]
In general, employers can’t avoid fulfilling their OHS duties by delegating them to someone else. However, in some jurisdictions, so-called prime contractors or constructors may be able to assign some safety duties to contractors working for them. But in such arrangements, it’s critical that the contract clearly spell out who’s responsible for which safety duties, such as supervising workers at the site.
Example: An employer supplied a crane, along with an operator and rigger, to a prime contractor and established a safety zone for the crane’s work. The prime contractor directed the employer’s workers to operate the crane outside this zone, causing the crane to come into contact with an energized power line. The employer was penalized for failing to provide adequate supervision.
The BC Workers’ Compensation Appeals Tribunal rejected the employer’s argument that the prime contractor was responsible for supervising the workers at the time of the incident. The employer failed to clearly communicate who would be responsible for supervising these workers. The Tribunal said, “In the absence of such clear communication, a vacuum could develop in which each party might assume the other was undertaking the responsibility for supervision of the workers.” It concluded that “the more specialized and potentially hazardous the equipment being provided, the greater is the employer’s responsibility to ensure that adequate supervision will be maintained in respect of its workers.” Here, the employer failed to exercise due diligence because it essentially abdicated its responsibilities for supervision once the crane was rented by the prime contractor [WCAT-2014-01871].
[/learn_more]
[learn_more caption=”Lesson #16: You Need a System to Ensure Compliance of Contractors”]
If you use contractors, you must have a system in place to ensure that they’re complying with the terms of the contract, applicable safety rules and the OHS laws. That system should address contractor safety in general and safety as to the particular worksite or job for which you’ve retained the contractor. (See, Contractors Compliance Centre) If one of your contractors subsequently commits a safety violation while working for you, the government may be able to go after not only the contractor for its violation but also you if you didn’t take steps to ensure its compliance.
Example: At a residential construction site, a painting sub-contractor held a ladder in place while a worker climbed it. Neither were wearing fall protection. So when the ladder became unstable, both fell and suffered minor injuries. The prime contractor for the site was penalized for OHS violations.
The BC Workers’ Compensation Appeals Tribunal rejected the prime contractor’s due diligence defence and its argument that the painting sub-contractor was the party at fault. The Tribunal explained that the prime contractor had to have both a general system for overseeing contractors as well as specific systems relevant to that particular site and specific contractor. Although this prime contractor had a general oversight system, it didn’t effectively oversee this site and this sub-contractor. It simply told the painting sub- contractor what his duties were but didn’t otherwise supervise him. And because the sub-contractor had performed satisfactorily on other jobs, it simply assumed he’d engage in appropriate conduct as this site. The Tribunal concluded that it’s a “matter of general knowledge that contractors in the work place are sometimes not motivated or interested in complying with their safety obligations. It is for this very reason that multi-employer jobsites place an added supervisory duty on the prime contractor, who is in the best position to control and ensure safety” [WCAT-2013-03358].
If you have an effective contractor oversight system in place, you’re less likely to be held liable if your contractors commit safety offences.
Example: The court in Bay Grenville, discussed above, exonerated the constructor for the safety violations committed by a subcontractor. It praised the constructor for its system of overseeing contractors and sub-contractors, which included:
- Agreements that required contractors and sub-contractors to comply with the OHS laws and regulations and its project-specific safety requirements;
- A safety manual developed specifically for this project and given to all contractors and sub-contractors;
- The retention of a site superintendent to manage the project and be a constant presence on site to deal with contractors, sub-contractors and safety issues; and
- Random weekly site inspections to identify hazards.
[/learn_more]
[learn_more caption=”Lesson #17: Contractors Also Require Adequate Supervision”]
As with workers, you can’t assume that contractors will comply with safety rules and OHS regulations. That’s why a key element of a contractor oversight or management system is supervision of contractors to ensure their compliance.
Example: A worker for a window cleaning company hired to clean a hotel’s glass canopy fell from the canopy and died. She wasn’t wearing fall protection at the time. The hotel was penalized for an OHS offence. The BC Workers’ Compensation Appeals Tribunal rejected the hotel’s due diligence defence. As the prime contractor, the hotel had a duty to coordinate health and safety in this multi-employer workplace. But the hotel didn’t have a system for ensuring that contractors complied with the OHS laws or supervise them, which was “troubling given the number of contractors it uses in and around its hotel,” noted the Tribunal. For example, the Tribunal said the hotel should’ve had an auditing system to ensure ongoing contractor compliance and conducted spot checks of contractors [WCAT-2014-00711 (Re)].
[/learn_more]
[learn_more caption=”Lesson #18: Don’t Deviate from Specific Safety Plans”]
In some circumstances, you may be required to develop specific safety plans, such as a fall protection plan, that address safety hazards and issues at a particular site or for a particular activity. But such plans are only effective if supervisors and workers actually comply with them. Deviating from a safety plan is likely to undermine your due diligence defence.
Example: At a multi-story housing development site, the roofing company had a fall protection plan in place that required the installation of guardrails and anchors. But the prime contractor didn’t install the guardrails or anchors. So the roofing company’s supervisor drew up by hand an alternate plan that relied on the use of work zones instead. However, after a safety officer saw workers on the roof without fall protection, the roofing company was penalized for fall protection and other safety violations.
The BC Workers’ Compensation Appeals Tribunal rejected the company’s due diligence defence and its argument that the prime contractor was to blame for the violations. Yes, the prime contractor was at fault for not installing the guardrails and anchors as required by the fall protection plan. But when the company’s crew arrived and found that these safety measures hadn’t been installed, the supervisor shouldn’t have deviated from the original safety plan and created an ad hoc plan on the scene. Rather, he should’ve contacted the prime contractor and found out when this equipment was going to be installed, made other arrangements for its installation or refused to let the crew work on the roof until the equipment was installed [WCAT-2014-00065].
[/learn_more]
[learn_more caption=”Lesson #19: Duties to Workers Apply Outside of Your Workplace”]
An employer’s duty to ensure the health and safety of its workers applies when they’re working not only in a workplace controlled by the employer but also at other sites owned or controlled by other employers.
Example: In Reliable Wood, the truck driver died while unloading wood shavings from a silo located at a flooring company’s site. His employer argued that it wasn’t liable because the danger was located at the workplace of a third party (the flooring company). But the court noted that the flooring company wasn’t involved in any aspect of removing the material from the silo. And the dangerous procedure used to do so was developed by the employer—not the flooring company. The court concluded that even if the flooring company bore some responsibility for the driver’s death, that didn’t relieve the employer of its duty. Moreover, if the employer thought that the flooring company’s equipment posed a hazard to its workers, it should’ve insisted that the company address the hazard (such as by installing a vibrator) or refused to send its workers into this dangerous situation, added the court.
[/learn_more]
[learn_more caption=”Lesson #20: Senior Management Must Lead by Example”]
Members of senior management must set an example for supervisors and workers when it comes to workplace safety. They effectively set the tone and lay the foundation for the safety culture. And it’s not enough for company owners, directors, etc. to simply ensure that a robust and effective OHS program is in effect—they must also lead by example. In other words, actions speak louder than words.
Example: A safety officer saw workers for a roofing company—and the company’s owner—on a roof without fall protection. The company was issued an administrative penalty for several safety violations and appealed. The BC Workers’ Compensation Appeals Tribunal upheld the penalty. The company argued that it acted with due diligence to prevent violations of the fall protection requirements. But the Tribunal disagreed. For example, the company’s owner was supposed to be supervising the workers on the roof. But he himself wasn’t wearing fall protection at the time. And although the owner told workers that he’d fine them if they failed to use fall protection, these claims were merely empty threats—he never actually fined any workers [WCAT-2014-01444].
[/learn_more]
BOTTOM LINE
Exercising due diligence isn’t just about protecting the company from liability—it’s about protecting workers from injuries and preventing safety violations and incidents from happening in the first place. So to develop an effective and comprehensive OHS program based on due diligence principles, learn from the mistakes made by the companies in these cases—and model yourself on those companies that got it right.
SHOW YOUR LAWYER
R. v. Flynn Canada Ltd., [2013] O.J. No. 6232, Oct.. 31, 2013
R. v. Reliable Wood Shavings Inc., [2013] ONCJ 518 (CanLII), Sept. 18, 2013
R. v. Value Drug Mart Associates Ltd., 2014 ABPC 164 (CanLII), July 29, 2014
Ontario (Ministry of Labour) v. Anray Ltd., [2014] ONCJ 203 (CanLII), April 15, 2014
Ontario (Ministry of Labour) v. Bay Grenville Properties Ltd. et al., [2014] ONCJ 349 (CanLII), July 21, 2014
WCAT-2013-02380 (Re), [2013] CanLII 79016 (BC WCAT), Aug. 26, 2013
WCAT-2013-02499 (Re), [2013] CanLII 80043 (BC WCAT), Sept. 9, 2013
WCAT-2013-02719 (Re), [2013] CanLII 80619 (BC WCAT), Sept. 30, 2013
WCAT-2013-03241 (Re), [2013] CanLII 79442 (BC WCAT), Nov. 21, 2013
WCAT-2013-03358 (Re), [2013] CanLII 80101 (BC WCAT), Nov. 29, 2013
WCAT-2013-03550 (Re), [2013] CanLII 95360 (BC WCAT), Dec. 19, 2013
WCAT-2013-03580 (Re), [2013] CanLII 95347 (BC WCAT), Dec. 20, 2013
WCAT-2014-00065 (Re), [2014] CanLII 44439 (BC WCAT), Jan. 10, 2014
WCAT-2014-00128 (Re), [2014] CanLII 44604 (BC WCAT), Jan. 16, 2014
WCAT-2014-00331 (Re), [2014] CanLII 44460 (BC WCAT), Jan. 31, 2014
WCAT-2014-00457 (Re), [2014] CanLII 43942 (BC WCAT), Feb. 13, 2014
WCAT-2014-00554 (Re), [2014] CanLII 45748 (BC WCAT), Feb. 21, 2014
WCAT-2014-00711 (Re), [2014] CanLII 45714 (BC WCAT), March 6, 2014
WCAT-2014-01444 (Re), [2014] CanLII 42351 (BC WCAT), May 13, 2014
WCAT-2014-01871 (Re), [2014] CanLII 42633 (BC WCAT), June 20, 2014
Yukon (Director of Occupational Health and Safety) v. Yukon Tire Centre Inc., [2014] YKTC 4 (CanLII), Jan. 29, 2014
[box]
6 KEY FACTS ABOUT DUE DILIGENCE
- There are two kinds of due diligence: reasonable steps and reasonable mistake of fact.
- Due diligence is a defence that must be proven by a company or individual charged with a safety violation on a balance of probabilities.
- Anyone charged with a violation of the OHS laws, including companies and individuals, can raise a due diligence defence.
- The due diligence defence applies to most violations of so-called “regulatory” laws, such as OHS and environmental laws.
- Although due diligence isn’t technically a defence to criminal negligence or “C-45” charges, proving that you exercised due diligence makes it impossible to be convicted of criminal negligence.
- Courts consider various factors when evaluating a due diligence defence, including foreseeability, preventability, control and degree of harm.
[/box]