Spot The Safety Violation: Make Sure Proper PPE Is Available
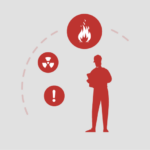
Can you think of a better way for this worker to protect his eyes’
Getting workers to wear PPE can be a challenge. And according to one poll of safety professionals on PPE, eye protection was found to be the ‘most challenging’ according to 42% of respondents, which isn’t surprising given that nearly three out of five workers who experienced eye injuries weren’t wearing eye protection at the time of the incident or were wearing the wrong kind of eye protection for the job.
So we should at least give the worker in this picture from the US Naval Safety Center credit for recognizing that using the saw posed a hazard to his eyes and trying to do something to protect them. But a plastic bucket isn’t appropriate eye protection. (And depending on how loud the saw is, he may need proper hearing protection, too.)
Failing to wear proper eye protection can cost workers’ their vision’and result in fines for employers. Example: A worker at an Ontario nursing home was seriously injured when a container of disinfectant accidently sprayed his eyes. He wasn’t wearing eye protection at the time. The nursing home pleaded guilty to failing to ensure that the worker wore appropriate eye protection when exposed to an eye hazard and was fined $55,000.
Protect Workers’ Eyes with 6 Steps
To ensure that workers’ eyes are protected from hazards and that the company complies with the requirements for eye protection in the OHS laws, implement a face and eye protection policy that reflects these six steps:
Step #1: Determine if there’s a risk of injury to workers’ eyes. Could they be exposed to dust, fibres, flying particles, tree branches, splashing fluids, radiation, etc.’ For example, there’s a risk of an eye injury to the worker in this picture caused by dust or particles kicked up by the saw he’s operating.
Step #2: Decide if you can eliminate or control these hazards. If you identify any hazards to workers’ eyes, you want to eliminate or control them first, such as by installing screens or guards around equipment to protect workers from flying particles or splashing liquids. You can also implement administrative measures, such as requiring workers to wet surfaces to keep down dust.
Step #3: Select appropriate eye protection. If you can’t eliminate or control the eye hazards, determine the appropriate kind of eye protection to shield workers from them. Which type of eye protection is appropriate will depend on the nature of the eye hazard. There are seven basic classes of eye protection:
- Spectacles;
- Goggles;
- Welding helmets;
- Welding hand shields;
- Non-rigid helmets or hoods;
- Face shields; and
- Respirator facepieces.
Once you’ve selected the appropriate eye protection, make sure that it’s available to the workers who’ll need it. Perhaps the worker in this picture had to improvise his own PPE because his employer didn’t provide him with the appropriate eye protection’
Step #4: Ensure workers use eye protection properly. Once you’ve selected appropriate eye protection and provided it to workers, make sure that they use it correctly. For example, eye protection should fit workers properly and not obscure their vision.
Step #5: Make sure workers properly maintain their eye protection. If workers don’t maintain their eye protection, it won’t adequately protect their eyes. So ensure that workers inspect their eye protection before using it, clean it when needed and properly store it.
Step #6: Train workers. As with any PPE, make sure to train workers on eye protection, including when it’s needed, how to use it and how to maintain it.