Mobile Devices In The Workplace Policy
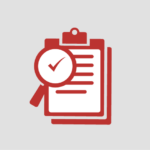
This Model Policy is based on Ontario OHS requirements but can be adapted for any other jurisdiction.
- PURPOSE
In recognition that continuous exposure to high levels of noise can result in hearing loss or damage, ABC Company has adopted this Hearing Conservation and Noise Protection Policy to protect workers from these hazards and ensure compliance with the requirements of Part 16 of the Alberta Occupational Health and Safety Code (“Code”), as well as the Occupational Health and Safety Act (“Act”), the OHS Noise Regulation (“Regulation”), the ABC Company Occupational Health and Safety Program (“Safety Program”), any ABC Company Noise Management Program (“Noise Management Program”) in effect, and other applicable requirements and standards.
- DEFINITIONS
For purposes of this Policy:
- “Attenuation” means a reduction in sound pressure level incident upon the ear;
- “Audiometer” means a device meeting the specifications for an audiometer set out in ANSI S3.6-2004, Specification for Audiometers
- “Competent person” means a person who: (a) is qualified because of knowledge, training and experience to organize the work and its performance; (b) is familiar with this Act and the regulations that apply to the work, and (c) has knowledge of any potential or actual danger to health or safety in the workplace
- “dBA” means a measure of sound level in decibels using a reference sound pressure of 20 micropascals when measured on the A-weighting network of a sound level meter
- “Decibel” “decibel” means a unit of measurement of sound pressure level equal to 20 times the logarithm to the base 10 of the ratio of the pressure of a sound, divided by the reference pressure of 20 micropascals
-
“Equivalent sound exposure level” means the steady sound level in dBA which, if present in a workplace for eight hours in a day, would contain the same total energy as that generated by the actual and varying sound levels to which a worker is exposed in his or her total work day. The equivalent sound exposure level is determined in accordance with the formula, in which:
- Lex,8 is the equivalent sound exposure level in 8 hours
- Σ is the sum of the values in the enclosed expression for all activities from i = 1 to i = n
- i is a discrete activity of a worker exposed to a sound level
- ti is the duration in hours of i
- SPLi is the sound level of i in dBA
- n is is the total number of discrete activities in the worker’s total workday
- “Hazardous sound level” means a sound level greater than an equivalent sound exposure level of 85 dBA, Lex,8
- “Hearing protection devices (HPDs)” means personal protective devices designed to reduce the level of sound reaching the eardrum
- “PPE” means personal protective equipment
- POLICY STATEMENT
ABC Company will take all measures reasonably necessary in the circumstances to protect workers from exposure to hazardous sound levels and ensure that no worker is exposed to a sound level greater than an equivalent sound exposure level of 85 dBA, Lex,8 by using engineering and other controls so that
workers’ will be protected without being required to use HPDs. However, HPDs will be required where engineering controls are not available to prevent exposure to hazardous sound levels for the reasons listed in Section 6.6 below.
- WORKERS THIS POLICY IS INTENDED TO PROTECT
The intent of this Policy is to ensure that all workers engaged to work at ABC Company work sites who are or may be exposed to hazardous levels of sound are properly protected regardless of who pays or employs those workers, including:
- Full- or part-time workers employed by ABC Company;
- Temporary employees placed by an outside agency to work at the site;
- Contract labourers engaged to perform work at the site;
- Volunteers who work at the site for free; and
- Workers employed by constructors, contractors, and subcontractors to perform work at the site under a contract with ABC Company.
- NOISE MEASUREMENT
- Noise Exposure Assessment
If reasonably necessary, ABC Company will designate an industrial hygienist, audiologist, or other competent professional to perform a noise exposure assessment of the workplace to determine Lex,8, i.e., the equivalent sound exposure level in 8 hours to determine whether workers are or may be exposed to hazardous sound levels. Measurements of sound levels in the workplace used to determine what protective measures are appropriate will be done without regard to any use of HPDs.
- Measurement Methods
For shift lengths that are greater or less than 8 hours, the Lex,8 will be calculated using the equation:
Lex,8= Leq, T +10 Log (T/8)
where T is the shift duration in hours. Where noise exposure can be easily split into discrete work activities during which sound levels are steady, the following Table 1 will be used to determine the Leq for the shift:
Table 1: Steady Exposure Maximum Duration
Steady Sound Level (dBA) | Duration |
82 | 16 hours |
85 | 8 hours |
88 | 4 hours |
91 | 2 hours |
94 | 1 hours |
97 | 30 minutes |
100 | 15 minutes |
103 | 7.5 minutes |
106 | 3.75 minutes |
109 | 1.88 minutes |
112 | 0.94 minutes |
115 | 28.12 seconds |
- Noise Exposure Limits
Where workers are exposed to a steady sound level throughout the shift, the duration of exposure will not exceed the value for the corresponding sound level in Table 1. Once the worker reaches the permissible duration for that sound level, the worker’s noise exposure will be deemed to have reached 100% of the permissible daily noise dose. Example: Two hours is the maximum permissible daily exposure duration for a worker exposed to a steady sound level of 91 dBA.
Where daily noise exposure consists of two or more periods of exposure of different levels, the following equation will be used to determine if the overall exposure exceeds the allowable noise exposure limits:
(C1/T1 + C2/T2 + …. Cn/Tn) x 100 = % of exposure limit Where:
- C = total duration of exposure at a specific noise level; and
- T = total duration of exposure permitted at that
The 85 dBA Lex,8 exposure limit is exceeded when the dose exceeds 100%.
- Noise Measurement Equipment
In performing the above assessments, the competent person will measure noise in accordance with CSA Z107.56-13, Measurement of Noise Exposure, using a:
- A sound level meter meeting at least the Type 2 requirements of ANSI S1.4 -1983 (R1997), Specification for Sound Level Meters or International Electrotechnical Commission (IEC), IEC 61672-1 Electroacoustics – Sound level meters, used on an A-weighting network and on slow response.
- A noise dosimeter with Type 2 tolerance under ANSI S1.25-1991, Specification for Personal Noise Dosimeters, ANSI S1.4 – 1983 (R1997), Specification for Sound Level Meters, or IEC 61672-1, Electro-acoustics – Sound level meters with an A-weighting network, a dynamic range of at least 50 dB, a crest factor capability of at least 30 dB and a threshold level at least 10 dB below the applicable criterion level (in this case, 75 dBA or less). Dosimeter settings should be: 85 dBA criterion level; 3 dB exchange rate and threshold no higher than 75 dBA (preferably zero).
- An integrating sound level meter that meets at least the Type 2 tolerance requirements of ANSI S1.4 – 1983 (R1997), Specification for Sound Level Meters, or IEC61672-1, Electroacoustics – Sound level meters , with an A-weighting network , a dynamic range of at least 50 dB, and a crest factor capability of at least 30 dB.
- Updating of Noise Exposure Assessment
ABC Company will ensure that the noise exposure assessment is updated if a change in equipment or process affects the noise level or length of time the worker is exposed to noise or in response to other indications that raise concerns about whether it is accurate or up to date, including but not limited to worker complaints or reports of symptoms associated with hearing damage.
- Records of Noise Exposure Measurements
ABC Company will ensure that the results of noise exposure measurements are recorded and list:
- The dates of measurements
- The workers or occupations evaluated
- The type of measuring equipment used
- The sound level readings measured AND
- The work location evaluated
Copies of the results of the noise exposure assessment will be made available upon request to:
- Affected workers, either directly or via the workplace Joint Health and Safety Committee or Health and Safety Representative AND
- Ontario Ministry of Labour and other government inspectors and officials
- CONTROL OF NOISE HAZARDS
- Selection of Controls—General Approach
Where ABC Company determines that workers are or may be exposed to hazardous sound levels, it will will implement appropriate following the the “hierarchy of controls” approach Company required by Section 2(2) of the Regulation in the following order of preference.
- Elimination
First preference will be given to total elimination of noise hazards, such as by total removal of dangerously loud machinery and equipment or substituting less noisy alternatives.
- Engineering Controls
Where elimination or substitution is not practicable, emphasis will be given to implementing engineering controls, that control sound hazards at the source or along the path of transmission to the worker. Examples of at-the-source engineering controls that ABC Company may consider include:
- Redesigning, modifying or retrofitting equipment, e.g., via installation of mufflers or noise damping materials;
- Replacing worn parts that are a source of noise; and/or
- Relocating noisy machinery and equipment.
Examples of along-the-path engineering controls that ABC Company may consider include:
- Installing sound-absorbing materials in or enclosing noisy work areas; and/or
- Screening or shielding noisy equipment.
- Work Practices & Administrative Controls
ABC Company will consider use of work practices ehere engineering controls are not practicable or effective or as a supplement to engineering controls, which may include:
- Modifications to work schedules to limit how long workers are exposed to noise; and/or
- Preventive maintenance to minimize noise created by machinery and equipment.
- Warning Signs
In accordance with Section 2(7) of the Regulation, where practicable, ABC Company will ensure that at every approach to a workplace area where the measured sound level regularly exceeds 85 dBA, a clearly visible warning sign is posted that:
- Warns of hazardous sound levels;
- Lists the actual sound level in dBA ;
- States and/or uses icons to indicate thtat hearing protection must be worn in the area; and
- Lists the maximum allowable exposure duration for the area without hearing protection.
- PPE & HPDs
In accordance with Section 2(6) of the Regulation, ABC Company will emphasize engineering controls and rely on mandatory worker use of PPE in the form of HPDs as the principle form of protection against hazardous sound levels only when engineering controls:
- Do not exist or cannot be obtained;
- Are not reasonable or practical to adopt, install or provide due to the duration of frequency or nature of the process, operation or work;
- Are rendered ineffective due to temporary breakdown of such controls; or
- Are ineffective to prevent, control or limit exposure because of an emergency.
- SELECTION, USE & MAINTENANCE OF HPDs
- General Principles
Where ABC Company does rely on worker use of HPDs as protection against hazardous noise levels, its selection, use and maintenance will be in accordance with CSA Z94.2-14,Hearing Protection Devices – Performance, Selection, Care, and Use.
- HPD Selection
As required by Section 4(1) of the Regulation, in selecting a hearing protection device ABC Company will consider:
- The sound levels to which a worker is exposed;
- The attenuation provided by the device; and
- Information from the manufacturer regarding the device’s use and limitations.
HPD selection will also consider the following factors:
- The physical characteristics of the workers who will be wearing the device;
- The device’s compatibility with other safety equipment;
- Temperature, humidity, air pressure, and other relevant workplace conditions;
- How easy the device is to use and handle; and
- How the device affects the worker’s ability to communicate.
ABC Company shall ensure that HPDs meet CSA standards for appropriate class and grade as set out in Table 2 below:
Table 2: CSA Class & Grade HPD Criteria
Maximum Equivalent
Noise Level (dBA Lex) |
CSA Class of Hearing
Protection |
CSA Grade of Hearing
Protection |
≤ 90 | C, B, or A | 1,2, 3, or 4 |
≤ 95 | B or A | 2, 3, or 4 |
≤ 100 | A | 3 or 4 |
≤ 105 | A | 4 |
≤ 110 | A earplug +
A or B earmuff |
3 or 4 earplug +
2, 3, or 4 earmuff |
˃110 | A earplug +
A or B earmuff and limited exposure time to keep sound reaching the eardrum below 85 dBA Lex |
3 or 4 earplug +
2, 3, or 4 earmuff and limited exposure time to keep sound reaching the eardrum below 85 dBA Lex |
As indicated in Table 2, workers exposed to noise greater than 105 dBA Lex must use dual hearing protection—both earplugs and earmuffs.
- HPD Use & Maintenance
ABC Company shall ensure that HPDs are used and maintained in accordance with the instructions of the device’s manufacturer.
- [OPTIONAL] 8. AUDIOMETRIC TESTING
- What Audiometric Testing Will Be Provided
ABC Company will provide workers exposed to hazardous noise levels audiometric testing, at ABC Company expense, including:
- An initial baseline test as soon as practicable and no later than six months after the worker is employed or within six months after a worker becomes exposed to hazardous noise levels as a result of changes in work duties or conditions. Where practicable, baseline testing will be:
- Done after a minimum 12 hour period during which the worker is not exposed to any noise; and
- Conducted in a noise-free environment when the worker has been away from noise for 14 hours, including noise exposure away from work;
- Additional testing within 12 months of the initial baseline test; and
- Additional testing at least every 2 years thereafter.
- When Audiometric Testing Will Be Conducted
If practicable, the audiometric tests will be carried out during the worker’s normal working hours.
- How Audiometric Testing Will Be Conducted
ABC Company will ensure that audiometric tests are administered by an audiometric technician who will:
- Work in consultation with a physician, audiologist, or occupational health nurse designated by ABC Company;
- Maintain a log book for each audiometer used that:
- Contains the written calibration records of the audiometer; and
- Remains with the audiometer throughout its useful lifetime;
- Perform pure-tone-air conduction threshold testing of each air at 500, 1,000, 2,000, 3,000, 4,000, 6,000, and 8,000 Hz;
- Perform such tests in a location where background noise does not exceed the levels set out in Table 3 below:
Table 3: Permissible Background Noise Conditions during Audiometric Testing
Octave Band Centre Frequency (Hz) | Maximum Noise Level (dB) |
500 | 22 |
1,000 | 30 |
2,000 | 35 |
4,000 | 42 |
8,000 | 45 |
- Records of Audiometric Testing
The audiometric technician who performs the required audiometric tests on workers will:
- Record the results of the audiometric tests performed;
- Give the worker a copy of the test results;
- Keep the audiometric test records for at least 10 years;
- Ensure that the medical history information is under the sole control of the consulting physician, audiologist, or occupational health nurse designated by ABC Company referred to in the first item above.
- What Happens If Tests Show Abnormal Audiograml/Abnormal Shift
Where the audiometric test results indicate an abnormal audiogram or show an abnormal shift, the audiometric technician will:
- Advise the worker of the test results;
- Ask the worker to provide relevant medical history—workers asked to provide a medical history must do so; and
- Forward the results, relevant medical history, and a baseline audiogram to the physician or audiologist designated by ABC Company to receive this information.
- What Happens If Abnormal Audiograml/Abnormal Shift Is Confirmed
Where the physician or audiologist designated by ABC Company confirms the audiogram as being abnormal or as showing an abnormal shift, the designated physician or audiologist will:
- Advise the worker of the confirmation within 30 days;
- Give the worker’s physician the results of the audiometric tests—as long as the worker provides written consent to do so; and
- Keep the audiometric test records for at least 10 years.
- Confidentiality of Worker’s Medical Information
Audiometric test records conducted under this Policy and the medical history provided by the worker. will not be released to any third persons unless the worker provides written consent (except insofar as such release is required by this Policy or the law).
- TRAINING & INSTRUCTION
Workers exposed to hazardous levels of noise will be trained in the proper selection, maintenance, and use of required hearing protection devices. Such training will include (without limitation):
- The hazards of exposure to excessive noise;
- How hearing protection protects them from such exposure;
- The capabilities and limitations of particular types of hearing protection devices used;
- The importance of ensuring a tight and comfortable fit;
- How to effect a tight seal between earplugs and the ear canal;
- How to effect a tight seal between earmuffs and the side of head;
- How to inspect the equipment;
- How to clean, disinfect and maintain the equipment;
- Why it’s important not to modify the equipment, such as by drilling holes in earcups.
- CONSTRUCTORS, CONTRACTORS & SUBCONTRACTORS
ABC Company will ensure that any prime constructors, contractors, and subcontractors hired to perform work involving exposure to hazardous levels noise at its work sites are, before such work begins:
- Notified about the noise hazards at the site and the dangers they pose;
- Required to ensure that all of their affected workers are provided and properly trained and instructed to use the hearing protectors required for such noise levels under this Policy;
- [Optional] Notified of the hearing testing provided by ABC Company to workers .
Constructors in control of project work at an ABC Company site that involves exposure to hazardous noise levels will be required to provide exposed workers engaged in the contract work adequate protection against those hazards by applying either:
- This Policy; or
- An equivalent policy and noise management program that meet the requirements of the Regulation.
- EVALUATION
This Policy will be reviewed, in consultation with the workplace Joint Health and Safety Committee, Health and Safety Representative, or, where no Committee or Representative exists, directly with workers at the site who are exposed to excessive noise, at least once a year and immediately in response to:
- Worker complaints or symptoms indicating ringing in the ears or hearing loss due to exposure to excessive noise;
- Changes to equipment, machinery, tools, or work conditions that increase or have the potential to increase either:
- How much noise the worker is exposed to; or
- The length of time the worker is exposed to excessive noise;
- Before the construction of significant additions or alterations to a work site that have the potential to create noise hazards; and
- Any other indications suggesting that this Policy might be ineffective or not responsive to current work site conditions and noise