How to Improve Safety in the Oil & Gas Sector—and Your Company
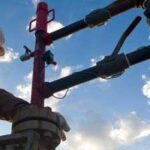
The Canadian National Energy Board (NEB) recently released a paper on how companies in the oil and gas sector can improve their safety and environmental management. The impetus for the paper was several recent high-profile environmental incidents in the industry, including the spill from the BP well in the Gulf of Mexico and pipeline ruptures in Alberta, Michigan and California.
Although the paper is geared toward oil and gas companies, it also provides valuable insight that can be useful to companies in other industries.
The NEB suggests that there are three key areas in need of improvement:
Corporate leadership and safety culture. The paper says that one of the causes of major incidents in this sector is the failure of senior corporate leadership to take an active role in the management of safety in their company’s operations. Senior corporate leadership can have a profound influence on the establishment and maintenance of a healthy safety culture. In fact, leaders who take an active role in overseeing the safety of the company’s operations set the stage for a culture of safety throughout the organization.
Effectiveness of management systems. Many companies find it difficult to effectively implement safety management systems. According to the NEB, such systems are only effective when they’re consistently applied, highly integrated and assign accountability.
Performance measurement and its role in hazard identification and risk mitigation. Many high hazard industries define and measure the safety of their operations based on the health and safety of individual workers. This approach to safety performance measurement has two principal short-comings:
- It places a lot of attention on “slip, trip, and fall” hazards, which may limit awareness of other hazards and risks that need to be managed; and
- It’s one-dimensional and provides an incomplete and inaccurate account of the overall level of safety of an activity, facility or organization.
Focusing on personal injury data while limiting or excluding information related to process safety and corporate culture can have catastrophic effects, says the paper. To get a more complete picture of safety performance, the NEB recommends that companies look beyond lagging indicators such as lost time injury rates to identify performance measures that promote more effective and comprehensive hazard identification and risk assessment.
Evaluate Your Own Company’s Safety Management
The NEB paper suggests that you use the following questions to stimulate discussion within your company about its own safety management:
- As a senior leader, how do you manage the business risk of a major incident’
- How does safety and environmental management factor into your internal corporate scorecard’ What percentage of your compensation is directly impacted by these targets’
- What barriers exist to corporate leaders actively managing safety and environmental protection’ How can these barriers be removed’
- How can industry move forward as a whole on corporate governance for safety’
- How can regulators improve requirements that will stimulate the development and maintenance of safety cultures’
- How does your current organizational structure enhance or detract from an integrated and comprehensive approach to safety management’
- How could your company safety management system be better integrated with your operational programs and other business functions to enhance safety outcomes’
- How can consistency of safety management system implementation across regions, activities, facilities and programs be facilitated’
- Are there opportunities to enhance risk management within your operation as a result of improved communication and coordination across business units or defined areas of expertise’ How can these opportunities be leveraged to advance overall safety’
- How could regulations and guidance be improved to obtain more effective implementation of safety management systems’
- How does your organization measure the safety of its operations’ What’s included’ What’s excluded’
- What leading and lagging indicators would provide the greatest visibility of overall safety’
- What does your choice of safety performance indicators communicate to workers’ Are there possible cultural implications to your use of certain measures’
- How can your company better detect latent threats to safety such as those posed by organizational factors’ Can your organizational structure be modified to improve safety outcomes’
- How could the performance indicators currently used by your regulator be improved to reflect appropriate safety performance measurement’